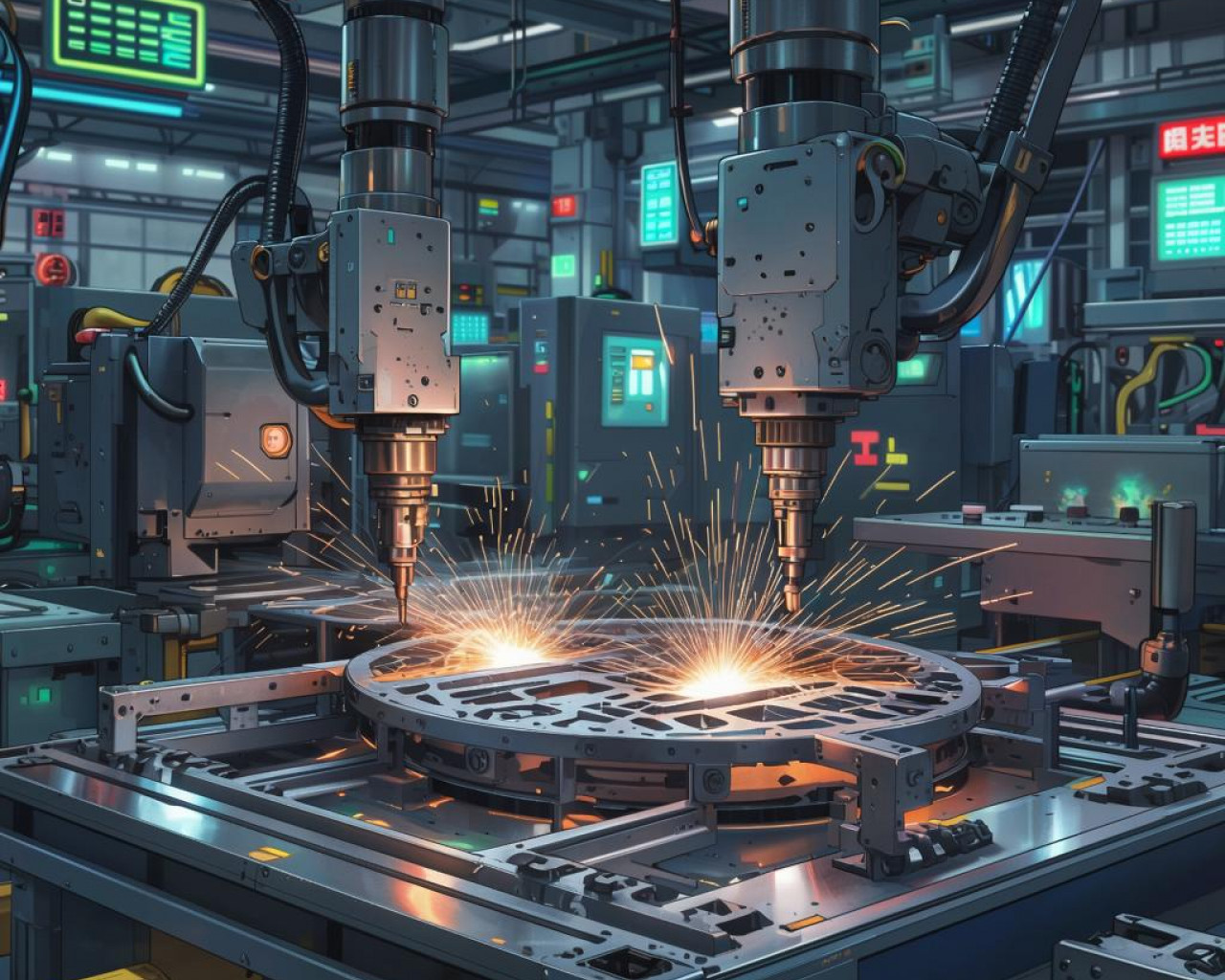
Почему стоит выбрать автоматизированную плазменную резку для производства металлических конструкций
Для качественного соединения металлов в условиях домашней мастерской или мелкосерийного изготовления оптимальным решением является приобретение современного MIG/MAG-устройства, построенного на базе силовой IGBT- или MOSFET-транзисторной схемы. Такое оборудование обеспечивает стабильность дуги и высокое качество шва, недостижимое для устаревших трансформаторных аналогов, при этом потребляя на 25–30% меньше электроэнергии. Его малый вес, обычно в пределах 8–20 кг, и компактные габариты позволяют легко перемещать аппарат по рабочей зоне и не требуют отдельного места для стационарного хранения.
Принципиальное отличие этих устройств заключается в методе преобразования тока. Вместо громоздкого низкочастотного трансформатора, работающего на 50 Гц, здесь используется высокочастотное преобразование (20-100 кГц). Это позволяет не только радикально уменьшить массу и размеры силового блока, но и получить почти идеальную вольт-амперную характеристику. На практике это означает мгновенный и легкий поджиг дуги, минимальное разбрызгивание металла и формирование равномерного, эстетически привлекательного шва даже у оператора с небольшим опытом. Фактически, современный аппарат для дуговой плавки в среде защитного газа делает процесс соединения металла более предсказуемым и контролируемым.
Технологическое превосходство: Что скрывается за компактным корпусом?
В основе работы аппарата с инверторной схемой лежит принцип двойного преобразования энергии. Входящее переменное напряжение сети (220В или 380В) сначала выпрямляется, а затем преобразуется высокочастотным модулем в переменное напряжение с частотой в десятки килогерц. Только после этого миниатюрный силовой трансформатор понижает напряжение до рабочего уровня (15–30 В), и финальный выпрямитель формирует постоянный ток для горения дуги. Весь этот процесс управляется микропроцессором, который считывает параметры дуги тысячи раз в секунду и мгновенно вносит корректировки.
Такой сложный, на первый взгляд, алгоритм дает ощутимые практические результаты. Стабильность дуги не зависит от колебаний напряжения в сети в пределах 15-20%, что является частой проблемой в частных сетях или при работе от генератора. Микропроцессорное управление позволяет реализовать функцию синергетической настройки (Synergic). Оператору достаточно указать тип проволоки, газа и толщину свариваемого металла, а аппарат автоматически подберет оптимальные значения напряжения и скорости подачи проволоки. Это кардинально сокращает время на подготовку и минимизирует риск прожога тонкого металла или получения непровара на толстом.
Преимущества в домашней мастерской: От ремонта забора до кастомного проекта
В контексте личного использования, где задачи варьируются от починки садового инвентаря до сборки металлической мебели или элементов автомобильного кузова, такое оборудование раскрывает свой потенциал в полной мере.
Компактность и мобильность: работайте где угодно
Трансформаторный агрегат весом 50-70 кг – это стационарная единица. Его перемещение превращается в отдельную задачу. Современное устройство весом 10 кг можно одной рукой перенести в любую точку участка, закинуть в багажник автомобиля для выездных работ или убрать на полку после использования. Это освобождает пространство в ограниченных условиях и дает свободу действий, не привязывая мастера к одному рабочему месту.
Энергоэффективность и работа от бытовой сети
Старые модели при работе на токах 140-160 А могли потреблять до 7-9 кВт, создавая серьезную нагрузку на бытовую электропроводку и вызывая срабатывание автоматов защиты. Аппарат с силовой электроникой при тех же параметрах тока потребляет 4-5.5 кВт. Это означает, что его можно без опасений подключать к стандартной розетке с автоматом на 16 А, не беспокоясь о "просадке" напряжения у соседей или перегрузке линии. Многие модели корректно функционируют от бензиновых генераторов мощностью от 5-6 кВт.
Простота освоения и качество шва
Для новичка настройка традиционного аппарата – это череда проб и ошибок. Синергетическое управление снимает эту проблему. Оно позволяет сразу получить качественный результат, фокусируясь на технике ведения горелки, а не на подборе параметров. Мягкая и стабильная дуга прощает мелкие ошибки, такие как колебания скорости или расстояния до детали, что позволяет быстрее наработать уверенные навыки и получать прочные, аккуратные соединения.
Масштабирование на промышленном уровне: Скорость, стабильность, экономия
Для коммерческого применения, где важны производительность и повторяемость результата, электронные MIG/MAG-системы предлагают иной набор преимуществ, напрямую влияющих на рентабельность.
Производительность и цикл работы (ПВ)
Продолжительность включения (ПВ), или рабочий цикл, – ключевой параметр для серийной работы. Он показывает, сколько времени из 10-минутного цикла аппарат может работать на заданном токе без перегрева. Профессиональные модели обеспечивают ПВ на уровне 60% при токах 250-300 А и 100% при токах до 200 А. Это означает возможность непрерывной работы при наложении длинных швов на металлоконструкциях, что сокращает простои и увеличивает скорость сборки изделий.
Стабильность дуги и работа со сложными материалами
Многие промышленные аппараты оснащены дополнительными режимами, такими как PULSE и DOUBLE PULSE. Импульсный режим позволяет соединять тонколистовой алюминий и нержавеющую сталь с минимальным тепловложением. Это предотвращает деформацию и коробление деталей, а также позволяет получить шов с характерным "чешуйчатым" рисунком, не требующий дополнительной обработки. Двойной импульс еще больше расширяет контроль над сварочной ванной, что критично при работе в сложных пространственных положениях.
Снижение эксплуатационных расходов
Экономия складывается из нескольких факторов. Во-первых, прямое снижение счетов за электроэнергию благодаря высокому КПД (85-90% против 60-70% у трансформаторов). Во-вторых, сокращение расхода проволоки и защитного газа за счет минимального разбрызгивания. В-третьих, уменьшение трудозатрат на постобработку: стабильная дуга оставляет аккуратный шов, который практически не нуждается в зачистке щеткой или абразивным кругом. В сочетании с такими технологиями, как ЧПУ резка металла, это позволяет добиться максимальной эффективности и точности производства.
Критерии подбора оборудования: на что обратить внимание
Чтобы инвестиция в оборудование была оправданной, следует оценить несколько ключевых характеристик, исходя из предполагаемых задач.
- Максимальный ток. Для бытовых задач и работы с металлом до 4-5 мм достаточно аппарата на 160-180 А. Для уверенной работы с толщинами 6-8 мм и небольшого коммерческого использования потребуется модель на 200-250 А. Промышленные задачи требуют тока от 300 А и выше.
- Продолжительность включения (ПВ). Для эпизодических работ в мастерской хватит ПВ 30-40% на максимальном токе. Для ежедневной нагрузки на сборочном участке ищите модели с ПВ не менее 60%.
- Наличие синергетического управления. Для начинающих – это обязательная функция. Для опытных мастеров – удобный инструмент, экономящий время. Большинство современных аппаратов среднего ценового сегмента им оснащены.
- Дополнительные режимы. Если планируется работа с алюминием или нержавеющей сталью, наличие импульсного режима (PULSE) является решающим фактором. Режимы 2Т/4Т (двухтактный и четырехтактный режим работы кнопки горелки) удобны для коротких прихваток и длинных швов соответственно. Возможность MMA- (ручной дуговой) и TIG- (аргонодуговой) плавки расширяет функционал устройства.
- Надежность и сервис. Обращайте внимание на репутацию производителя, срок гарантии и наличие авторизованных сервисных центров в вашем регионе. Качественный аппарат – это долгосрочное вложение.
Распространенные ошибки и как их избежать
Даже самое технологичное оборудование не застрахует от ошибок, связанных с отсутствием опыта. Вот три наиболее частых промаха.
Ошибка 1: Покупка аппарата с недостаточной мощностью. Желание сэкономить приводит к приобретению модели на 120-140 А. При попытке соединить металл толще 3 мм такой аппарат не сможет обеспечить достаточный провар. Шов будет выглядеть приемлемо, но его прочность окажется крайне низкой. Решение: всегда берите аппарат с 20-30% запасом по мощности относительно ваших основных задач.
Ошибка 2: Игнорирование качества расходных материалов. Дешевая проволока с неравномерной намоткой и плавающим диаметром, некачественный защитный газ с примесями или забитый токосъемный наконечник могут свести на нет все преимущества дорогого аппарата. Дуга будет нестабильной, подача проволоки – прерывистой. Решение: используйте только качественные, проверенные расходники. Их стоимость незначительно выше, но они гарантируют стабильность процесса.
Ошибка 3: Неправильная настройка прижимного ролика. Слишком сильный прижим деформирует проволоку, и она застревает в наконечнике. Слишком слабый – приводит к проскальзыванию, и подача становится неравномерной. Решение: затяните прижимной ролик так, чтобы проволоку можно было остановить, плотно зажав ее пальцами в перчатке перед горелкой. Это оптимальное усилие.
Заключительный совет эксперта
Современное MIG/MAG-устройство – это мощный инструмент, который демократизирует процесс качественного соединения металлов. Он прощает многие ошибки новичков и открывает новые горизонты для профессионалов. Однако не стоит рассматривать его как "волшебную палочку". Фундаментальные знания о металлах, правильная подготовка кромок и, главное, практика остаются основой мастерства. Инверторная технология – это не замена навыкам, а катализатор их быстрого и эффективного развития.
Как инверторная технология влияет на стабильность дуги и качество шва при работе в гаражной сети
Принцип работы: ключевое отличие от трансформаторных моделей
Чтобы понять источник стабильности, необходимо рассмотреть внутренние процессы. В отличие от громоздких трансформаторных устройств, где переменный ток сети 220В с частотой 50 Гц напрямую понижается тяжелой медной обмоткой, агрегаты с силовой электроникой работают по более сложному, но эффективному алгоритму:
- Первичное выпрямление. Входящий переменный ток (AC) из розетки преобразуется в постоянный (DC) при помощи диодного моста.
- Высокочастотное преобразование (инверсия). Полученный постоянный ток подается на силовой модуль (обычно на IGBT или MOSFET-транзисторах), который под управлением микропроцессора снова преобразует его в переменный, но уже с очень высокой частотой – от 20 000 до 100 000 Гц (20-100 кГц).
- Понижение и финальное выпрямление. Этот высокочастотный переменный ток поступает на миниатюрный, легкий ферритовый трансформатор, где его напряжение понижается до сварочных значений (например, 20-30В). После этого он окончательно выпрямляется и подается на горелку.
Именно второй этап – высокочастотное преобразование – является технологическим сердцем и главным козырем таких аппаратов. Управляющий микропроцессор способен изменять параметры работы транзисторов (широтно-импульсную модуляцию, ШИМ) тысячи раз в секунду. Это позволяет ему действовать как сверхбыстрый стабилизатор.
Стабильность дуги при просадках напряжения: практический аспект
Рассмотрим типичную ситуацию в частной мастерской. Вы работаете с металлом, а сосед по боксу включает мощный компрессор или болгарку. Напряжение в сети моментально проседает с 220В до, скажем, 195В. Вот как поведут себя разные типы оборудования.
Трансформаторный агрегат: Падение напряжения на входе на 12% почти линейно снижает выходной ток. Дуга становится "вялой", нестабильной, начинает гаснуть. Металл плохо проплавляется, увеличивается разбрызгивание, так как капля не успевает оторваться и перенестись в ванну плавно. Оператор вынужден прекращать работу, либо шов получается дефектным (непровар, поры).
Агрегат с инверсией: Датчики на плате управления фиксируют падение входного напряжения. Микропроцессор в течение микросекунд дает команду силовому модулю изменить режим работы – увеличить ширину импульсов. Это компенсирует нехватку "силы" на входе, и на выходе, на горелке, ток остается точно таким, какой был выставлен на панели управления, например, 100 Ампер. Оператор чаще всего даже не замечает просадки в сети – дуговой разряд горит так же ровно и стабильно.
Роль микропроцессора и обратной связи
Система обратной связи – это контур, в котором контроллер постоянно "спрашивает" у выходных цепей: "Какой ток сейчас?". Получая ответ, он сравнивает его с заданным значением и немедленно корректирует работу транзисторов. Эта петля обратной связи работает с частотой в десятки килогерц, поэтому реакция на любые изменения – будь то просадка сети, изменение длины дуги оператором или скачок сопротивления на металле – происходит практически мгновенно. Это обеспечивает беспрецедентную эластичность дуги: она не обрывается, даже если рука оператора дрогнула и расстояние от сопла до детали изменилось.
Влияние стабильной дуги на формирование соединения
Устойчивость дугового разряда напрямую конвертируется в высокое качество металлического соединения и упрощение работы. Это проявляется в нескольких ключевых аспектах.
Минимальное разбрызгивание металла
Когда дуга нестабильна, перенос присадочной проволоки в сварочную ванну происходит хаотично, крупными каплями. Эти капли, отрываясь, создают хлопки и разлетаются в виде брызг, загрязняя деталь и рабочее пространство. Стабильная дуга, поддерживаемая цифровым управлением, обеспечивает мелкокапельный или даже струйный перенос. Проволока плавится равномерно, капли имеют малый размер и под действием электродинамических сил точно переносятся в ванну. Результат: чистый шов, который почти не требует последующей зачистки щеткой или абразивным кругом. Экономится время и расходные материалы.
Глубина провара и формирование валика
Колебания тока приводят к неравномерному тепловложению. Где ток просел – там непровар, где скакнул – риск прожога, особенно на тонколистовом металле. Постоянный, стабильный ток гарантирует одинаковую глубину проплавления на всей длине соединения. Это критично для несущих конструкций, где от прочности зависит безопасность. Валик шва получается ровным, чешуйчатым, с одинаковой шириной и высотой, что свидетельствует о высоком качестве процесса.
Работа с тонкими металлами: точность и контроль
При ремонте кузовных элементов автомобиля или изготовлении изделий из листовой стали толщиной 0.8-1.0 мм малейший избыток тока ведет к необратимому прожогу. Трансформаторные агрегаты слишком инертны и грубы для таких задач. Аппарат с электронной регулировкой позволяет выставить ток с точностью до ампера и быть уверенным, что он не "скакнет" вверх в самый неподходящий момент. Это открывает возможности для выполнения деликатных работ, которые ранее были доступны только более сложным технологиям.
Сравнительный сценарий: соединение профильной трубы 1.5 мм встык
- Задача: Сварить раму из профильной трубы 40х20х1.5 мм. Сеть в частном секторе, напряжение колеблется от 205В до 230В.
- Использование трансформаторного устройства: Начинаем процесс. Включается соседский насос. Напряжение падает. Дуга "садится", проволока начинает утыкаться в металл, образуя наплывы. Увеличиваем ток, чтобы компенсировать. Напряжение восстанавливается – и повышенный ток мгновенно прожигает тонкую стенку профиля. Результат – несколько испорченных заготовок и потерянное время.
- Использование MIG/MAG-устройства с инверсией: Выставляем ток, например, 70А и напряжение 18.5В. Начинаем работу. Те же колебания сети остаются незамеченными. Дуга горит мягко, с характерным "шипением". Шов ложится ровно, без брызг и прожогов. Весь процесс проходит предсказуемо и под полным контролем от начала до конца. Финальное изделие имеет аккуратный вид и высокую прочность соединения.
Таким образом, технология высокочастотного преобразования не просто улучшает комфорт работы. Она фундаментально меняет сам процесс, нивелируя главный недостаток бытовых и мелкоцеховых электросетей – их нестабильность. Это позволяет получать результат промышленного уровня даже в условиях обычного частного бокса.